Case Study – Lower Cost Automation Batch Processing of a Cassette Load Port System
Hine Automation Team
August 22, 2023
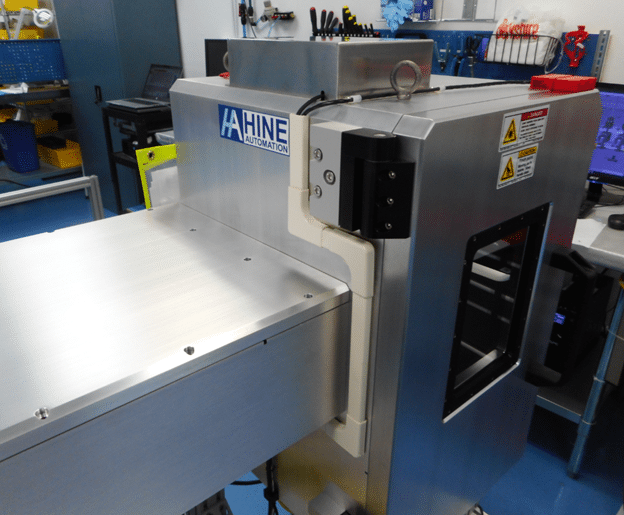
The semiconductor market continues to grow and place new demands on manufacturing. Therefore, innovation is essential for businesses that want to stay ahead of the competition and meet the needs of their customers.
Hine Automation is committed to continuous improvement and has a thorough understanding of the semiconductor automation market. Its success and ability to drive innovation are linked to an acute ability to listen to customers, identify pain points, and build creative solutions that address a specific product need.
As a leader in the industry, Hine has provided thousands of cost-effective solutions for OEMs. However, each product addresses a unique need and offers distinct functionality and integration per each customer’s technical and budgetary requirements. The SL-200C and SL-300C are no different.
Experience Drives Design and Sets the SL-200C and SL-300C Apart from Others
Although the SL-200C supports up to 200mm wafers and the SL-300C supports up to 300mm wafers, both combine two core competencies—the load lock handling arm and the vacuum elevator. Both are designed to run in a vacuum environment to transfer wafers in batches to the OEM’s process chamber.
Specifically, SL-200C and SL-300C operate with a vacuum cassette chamber and single-axis drive rail, making them an ideal option for OEMs who need a more cost-effective solution. Without a costly multi-axis robot, the end effector mounts to the drive rail and travels into and through the chamber allowing access to the Cassette Elevator and, when fully extended, into the process module. With this design, the System can map and locate wafers in the cassette, retrieve them, and then move them into a dedicated process module.
Together, they offer the market a low-cost solution for a cassette handling tool and a single process module setup that is easy to use and control.
Process More Wafers with Smaller Footprint
Designed for use in a clean room or similar environments, automated load locks function as an intelligent material handling subsystem by processing more wafers between loading cycles. The SL-200C and SL-300C are ideal for customers with a smaller footprint or cannot use a traditional cluster tool. Utilizing less size, the SL-200C and SL-300C can still provide the opportunity to use a full cassette of up to 25 wafers between chamber vents rather than venting after a single wafer run.
SL-200C, SL-300C Features:
- Reduced system footprint
- Up to 200mm (SL-200C) and 300mm (SL-300C) wafer handling capabilities
- Plug-and-play vacuum transport system
- High throughput with batch processing
- High vacuum environment compatibility
- Wafer-presence sensors
- Door interlock
SL-200C, SL-300C Configurations:
- Horizontal reach
- Substrate size
- Plumbing- standard vacuum or turbo
- Vertical motion mechanism- with or without Z-lift
- End Effectors- SEMI standard or custom
- Motor integration- under or side-mounted
- Slit Valves- SMC/VAT/Customer-supplied (MESC compatible)
- Payload- standard or high-load
Innovative Solution Delivers High Performance and Low Maintenance
Without the complexities of robotic machinery, there’s little maintenance. The SL-200C and SL-300C provide a drive rail with a single belt, offering high performance. Additionally, the cassette load port and automated load lock are designed to take up less room when every square foot of cleanroom real estate is critical.
About Hine Automation:
With deep experience in the semiconductor space, Hine’s technology and design development are consistently relevant to the evolving market. Whether in the very early stages of a customer’s project or modifying an existing solution, Hine sets the precedence of uncompromised quality and versatility in design and manufacturing.
For more information on Hine Automation, visit https://hineautomation.com/.