Hine Automation Pursues Reliability Excellence; First Test Robot Passes 10 Million Cycles
Hine Automation Team
May 19, 2022
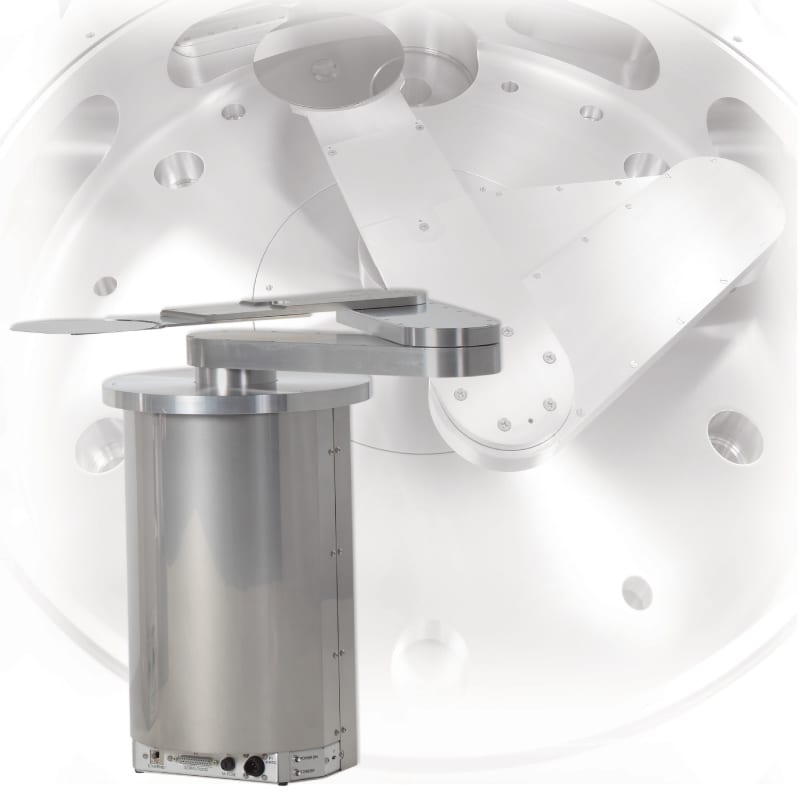
Hine Automation Pursues Reliability Excellence; First Test Robot Passes 10 Million Cycles
The constant pursuit of reliability excellence drives Hine Automation to perform at the highest levels. Hine continues to push the bar with innovation, creativity, education, and solutions critical to its customers’ success. Product performance predictability is vital. No surprises. No unplanned downtime. What lies ahead is known.
Setting the precedence of uncompromised quality in design and manufacturing sets Hine apart from other manufacturers. A willingness to push the bar and improve its state-of-the-art robotic components and automation systems lie at the forefront of Hine’s mission.
A Hine Automation robot fills but one part of a customer’s overall system. However, the robot acts as the core to transfer the raw materials across the system’s interfaces. Robot failure can force downtime and loss of production for weeks at a time. As a result, backlogs in parts availability, limited technical repair resources, and/or damage to related system assets can result in thousands of dollars in production cost. By looking ahead and knowing what breaks are likely to occur as a result of wear and tear operation, maintenance schedules can be adjusted to perform repairs before a failure occurs.
CHALLENGE
The challenge is how to improve the current level of reliability.
Robot Runs 10 Million Cycles and Counting
In early 2016, Hine Automation began reliability robot testing of one of its core products. Recently the robot exceeded expectations and passed 10 million cycles! As a result, more data was gathered for evaluation than originally expected as the original goal focused on only a few million cycles.
“This is a significant milestone for our company,” said Scott Craver, chief executive officer, Hine Automation. “Not many companies in our industry run any type of reliability testing, let alone one that extends 10 million cycles and counting.”
Craver states that several companies have the resources to gather the data, but it is not typically done to this level of testing. Calculating a mean time between failure and reliability, using theoretical values, is common, but actually running a test to see what’s possible, to really identify what the robot can withstand with greater accuracy of information, shows commitment to quality and reliability.
Raising the Bar—Gathering Essential Data
Identifying failures during testing was critical to improving the robot’s design. First, Hine conducted thorough evaluations when any error or inconsistent test result surfaced. Then, as needed, repairs were addressed, and the robot was put back into cycle testing. Engineering teams documented all errors and the associated test results with the appropriate robot design changes implemented to mitigate recurrence. The process was repeated until no more recurring errors occurred.
“We wanted the unit to fail,” said Karl Pearson, chief operating officer, Hine Automation. “We wanted to mimic conditions that the robot would see in production. If it didn’t fail, we wouldn’t have valid results to use when identifying improvements that could be made. The testing was accelerated and introduced to extreme conditions to create failures.”
Hine Automation wanted to identify the robot’s sensitivities and areas for improvement. Failures or errors were analyzed, and changes made to ensure a more robust solution.
Customers depend on reliability. When specifications state what a robot can withstand, Hine Automation can prove it beyond the traditional theoretical calculations that determine the failure rate and how long the specific part will last.
“Traditionally, a mathematical formula exists to provide a reliability calculation to estimate the timeline of a robot’s longevity,” said Craver. “We can run a test to show our customers exactly how long it will run before failure, and we can provide the supporting data points to reflect the timeline.”
Planning to Become Less Reactive
The most significant potential issues typically stem from unscheduled downtime. The ability to decide what needs to be maintained and when to schedule the maintenance allows for the freedom to manage production cycles and ensure operational deadlines are met.
It only takes one component to shut down an entire line of production. For example, an armband snaps and now the arm is drifting because the motor and arm are no longer connected. The arm then drifts into a slit valve or other valve which possibly closes and then breaks the end effector. Now multiple parts need replacement and, with this unscheduled downtime, production stops which significantly adds onto the overall expense associated with the issue. Additionally, the issue may not be about something failing. It could be a belt that starts stretching, and then, over time, the robot isn’t as accurate as it once was.
The intention of Hine Automation’s testing is to improve product design and help its customers determine when the robot would fail to ensure a more accurate maintenance schedule. For example, changing the oil in your car every 3,000 miles decreases the chance of engine failure but without service, breaking down on the way to work, leaving you in a bind right when you need to be at that important meeting, is an increasing possibility.
Armed with reliability data, you can line all those things up simultaneously, whether it’s an end effector or any other critical component and schedule all maintenance at the same time. It’s smarter than having a part randomly fail, causing the entire system to go down unexpectedly.
Putting Customers First
“You are not valued by the way you manage problems, but by the manner in which you prevent them, so we continuously strive to set the standard for reliability,” said Craver. “When you are reliable, you keep good data to make good decisions. You want to eliminate the shutdown of production. And to do that, you need to have a solid maintenance schedule to eliminate the sources of failures.”
Reliability and uptime have long been critical areas of focus for Hine Automation. The bar was further raised in 2016 when Hine found a better way to determine the life span of its robots, ensuring the highest level of functionality in the most extreme conditions. Continuous improvement is a CORE Hine Automation value. The constant pursuit of superior service is why Hine pushed this test robot beyond 10 million cycles, and forced awareness of the need to always be looking for new ways to improve.
Hine is a committed partner in the successful design and development of your customized solution, so when leveraging the expertise of Hine’s engineering department, your team can stay focused on its core competencies.
For more information about Hine Automation, visit our website at https://hineautomation.com/.