OEM Customer Leverages Hine Automation’s Depth of Experience to Improve Current Systems and Keep Processes Productive and Efficient
Hine Automation Team
February 1, 2023
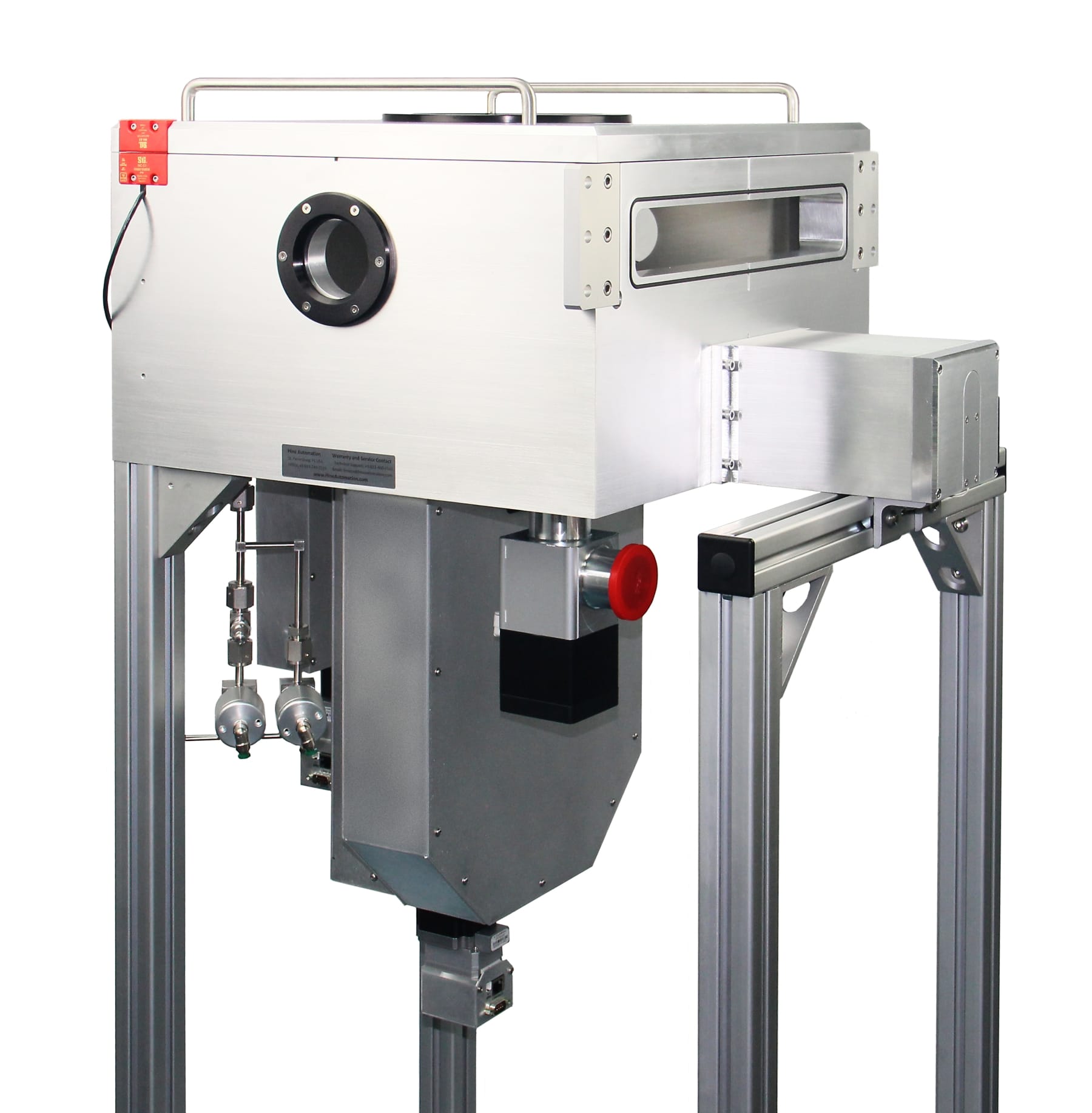
CHALLENGE
Customized Solutions to Address Size Restrictions
A leading OEM supplier and long-time customer needed to address throughput requirements. Due to industry-driven changes, this long-time customer approached Hine to develop a vacuum load lock to be integrated with a nitrogen glovebox with additional automation and larger capabilities. Specifically, the customer needed the vacuum load lock to interface with its existing tool using specific transfer height requirements.
Previous success with Hine’s automation tools made this choice easy for the OEM. Additionally, Hine’s proven engineering and design team continues to focus on relevant, current technologies. Combining efficiency in speed and quality and quickly adapting to the changing market conditions gave Hine the unique ability to meet the needs of this customer.
SOLUTION
Focus on Customer Need to Exceed Requirements and Goals
With vendor selection a high stakes operation, Hine recognizes the importance of quality and reliability. Unlike larger solution providers, Hine can offer flexibility in its offerings when it comes to customization needs.
Understanding the challenge the OEM faced, Hine’s experienced engineers created a solution to optimize performance and increase the company’s overall efficiencies.
Hine SL-300GBT
This customer had previously integrated Hine’s SL-200GBT on its 200mm tool which could be manually loaded. By adding the SL-300GBT to its product line, the customer can now handle 300mm substrates. The SL-300GBT can also handle smaller substrates if needed. Additionally, with the vacuum load lock, the OEM could load and process product without venting the process chamber to atmosphere, significantly improving throughput. Further, the built-in customization allowed the customer to interface Hine’s vacuum load lock to its tool without needing to make significant changes.
SL-300GBT features:
- Accessibility
- Safety Interlock
- Wafer Sensors
- Reduced System Footprint
- High Throughput Vacuum Transport System
- Ease of Operations
SL-300GBT Available Configurations:
- Telescoping drive rail with the ability to obtain standard reach requirements in a compact design
- Ability to process multiple wafers using a single drive rail unit
- Glovebox mounting flange with maintenance door and easy access for operators
- Ability to process higher loads than standard units due to robust drive rail
RELY ON HINE AUTOMATION
Relevant Technology, Reliability, and Expertise
Collaboration and customization are vital components when completing any project. Hine has a reputation for supporting long-term customers. Not only are its technology and design development consistently relevant, but the value the customer receives with service and support is unmatched.
Customers continue to rely on Hine for the latest industry solutions. However, success can only be achieved if both groups worked together with complete transparency. Custom engineering is essential, but Hine’s ability to listen and understand a customer’s needs means achieving a positive project outcome.
Benefits of a Customer-first Approach:
- Plug-and-play solutions
- Superior user experience
- Flexible and nimble
- Rooted in integrity and transparency
- Cost reduction
- Quality control
- Combined efficiency in speed and quality
About Hine Automation:
With more than 30 years of deep experience in the semiconductor space, Hine’s technology and design development are consistently relevant to the evolving market. Whether in the very early stages of a customer’s project or modifying an existing solution, Hine sets the precedence of uncompromised quality and versatility in design and manufacturing.
For more information on Hine Automation, visit our website: https://hineautomation.com/.